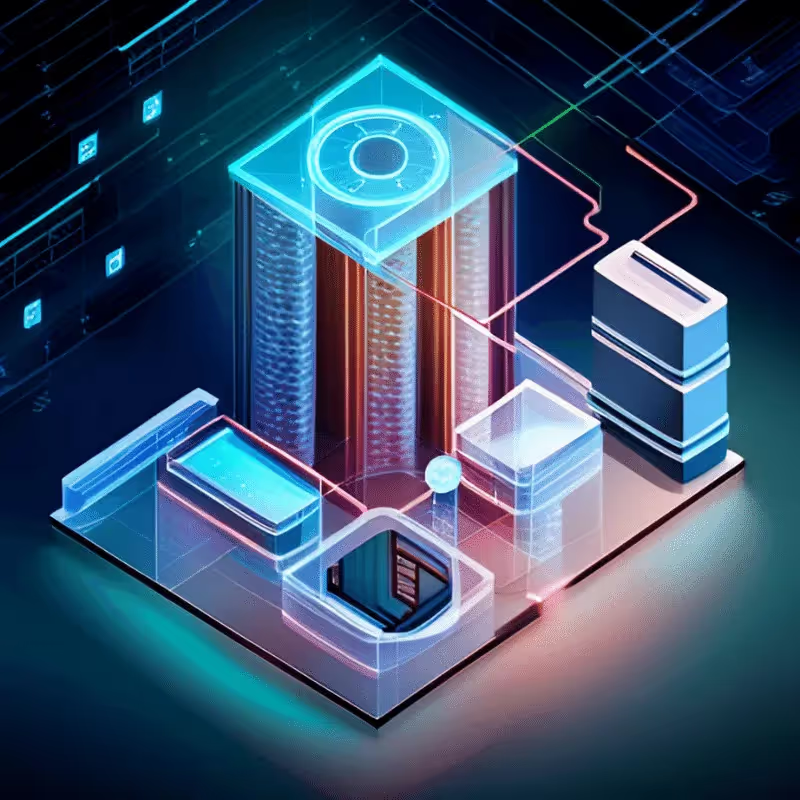
In recent years, the maintenance sector has witnessed a paradigm shift. Businesses across various industries are transitioning from traditional preventive maintenance to a more advanced, efficient predictive maintenance model, powered by Artificial Intelligence (AI). This shift is not merely a technological upgrade; it represents a fundamental change in approach — from routine schedules to data-driven decision-making.
The Rise of Predictive Maintenance:‍
‍Predictive maintenance leverages AI and machine learning to anticipate equipment failures before they happen. By analyzing data collected from sensors and machinery, AI algorithms can identify patterns and anomalies that often precede a breakdown. This approach is a stark contrast to preventive maintenance, which relies on scheduled maintenance regardless of the actual condition of the equipment.
Benefits of AI-Driven Predictive Maintenance:
- Reduced Downtime: Unplanned downtime can be costly. Predictive maintenance helps in identifying issues before they lead to equipment failure, thereby reducing the occurrence of unexpected operational halts.‍
- Extended Equipment Life: By addressing maintenance needs proactively, the lifespan of machinery and equipment is extended, maximizing the return on investment on expensive industrial assets.‍
- Cost Efficiency: Predictive maintenance optimizes maintenance tasks, leading to cost savings by reducing unnecessary maintenance activities and focusing resources where they are truly needed.‍
- Enhanced Safety and Compliance: Regular monitoring and maintenance ensure that equipment operates within the required safety standards, reducing the risk of accidents.
Azumo’s Implementation: A Case Study:
‍At Azumo, we recently partnered with a manufacturing client facing frequent and costly equipment downtime. Our approach involved:
- Custom Machine Learning Models: Developing AI models tailored to the client’s specific operational data and machinery.
- Real-time Data Analysis: Implementing IoT sensors to collect real-time operational data from equipment.
- Predictive Algorithms: Analyzing the data to identify patterns indicative of potential equipment failures.
The result was a staggering 40% reduction in equipment downtime and a significant improvement in operational efficiency.
Looking Ahead: The Future of Maintenance with AI:
‍As we move forward, the integration of AI in maintenance strategies is poised to become the norm rather than the exception. It’s a move towards smarter, more efficient operations that can significantly impact a company’s bottom line and operational sustainability.
The era of predictive maintenance, powered by AI, is here, and it’s transforming the way businesses approach equipment maintenance. It's an exciting time for companies like Azumo, as we lead the charge in helping businesses adopt these advanced technologies. The future is predictive, and it’s filled with possibilities for enhanced efficiency, cost savings, and operational excellence.